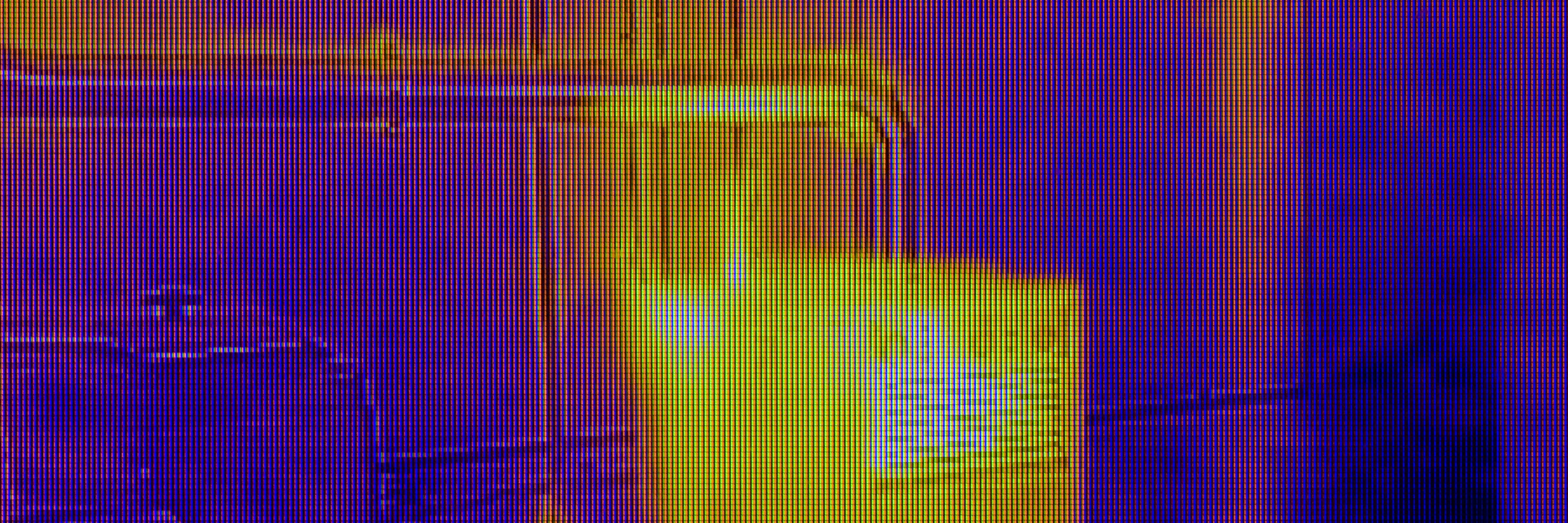
Thermography: Looking at
equipment inside and out
Blog
properties.trackTitle
properties.trackSubtitle
It’s frustrating when a piece of machinery starts to underperform. You know that something's not quite right but you can't put your finger on the exact cause. Identifying and rectifying equipment issues before they become problems is a critical part of averting loss, maintaining uninterrupted service, and reducing equipment operation costs.
Routine inspections and preventive maintenance can reduce failures, but they cannot reliably identify trouble spots. But what if you could identify and repair a potential fault before it even became a fault? By using a crystal ball? Unnecessary! What if an engineering inspection allowed you to see 'inside' your equipment, making the seemingly invisible visible? An infrared thermographic survey can help, stopping small issues from becoming big disasters.
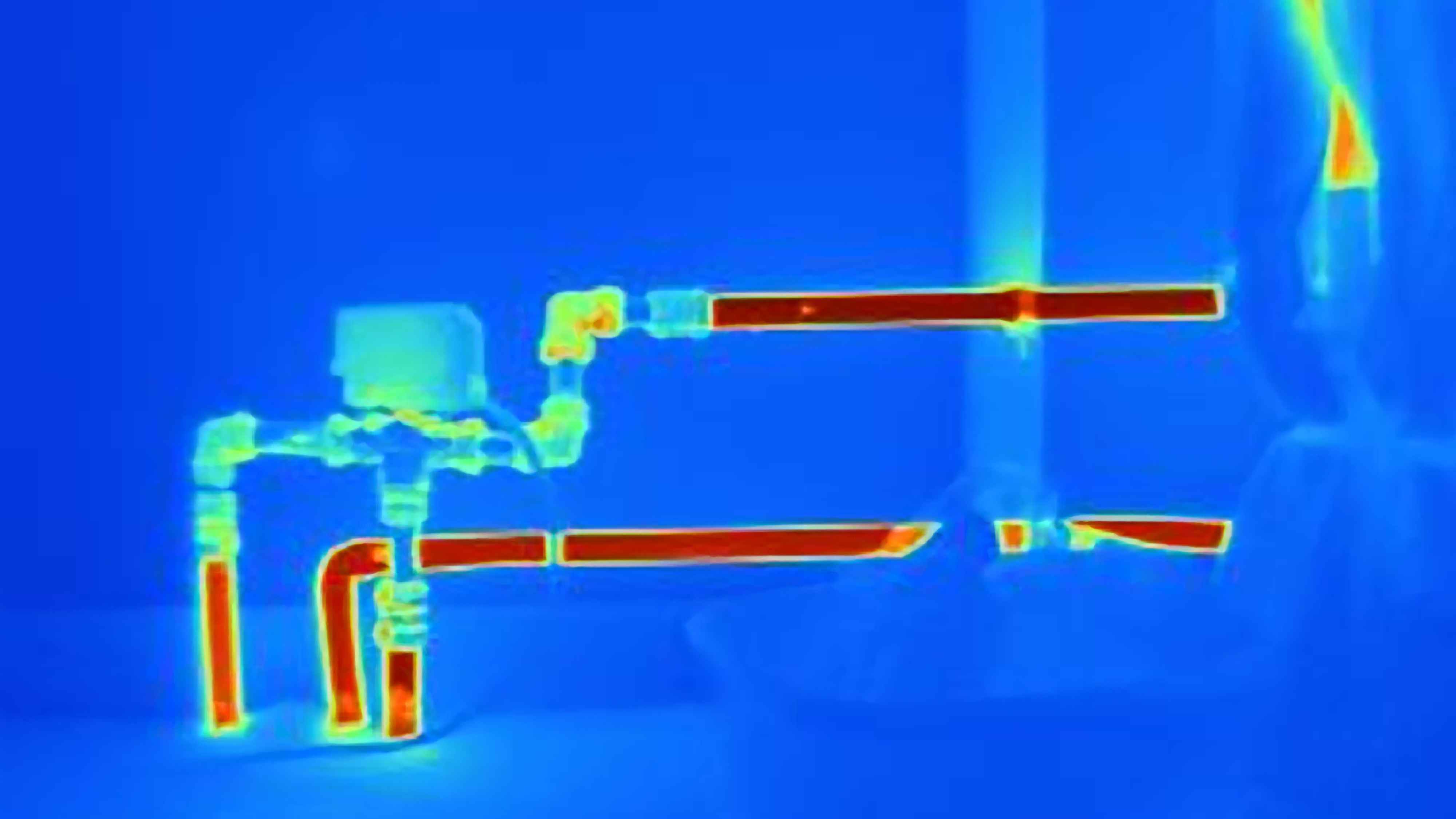
What is thermography?
Thermography works by using an infrared video camera (sensitive to thermal radiation) to detect and measure the temperature variations between surfaces in order to find any thermal anomalies. The camera converts the information into a thermographic image that shows a heat signature, meaning we can actually 'see' problems.
What are the benefits of a thermographic survey?
Unexpected breakdowns can bring production and/or services to a halt, affect a business's bottom line, cause power outages, and even result in fires. A thermographic survey provides equipment condition monitoring to ensure good equipment asset health, and can help to detect what repairs are needed before a breakdown even occurs. This offers the more cost-effective option of repair rather than replace; potentially saving businesses up to 20 times as much as the initial cost of the survey.
A thermographic survey also provides the opportunity to identify and acquire any needed replacement parts ahead of time, and doesn’t even require any equipment shutdown time. In fact, any distressed areas are measured with greater accuracy when the equipment is operating near full-load capacity.
It's not just about heat
Excessive heat is most commonly caused by resistance. This can be due to a number of things: poor electrical connections, overloading, improperly-sized components or a load imbalance. Not only can a thermographic survey alert you to this, it can also detect mechanical issues that are friction-related, such as improper lubrication or misalignment.
But it’s not just heat that thermography can detect.
A leak detection survey can help identify and rate any leaks that might be present within steam, compressed air and also refrigeration systems. This will highlight where there's energy loss and also identify any faulty/defective steam traps and heat transfer. This can be applied to blockages, steam and general pipework too.
As an illustration, for every pound spent on a thermographic survey, five pounds in cost avoidance is identified on the damage. When considering factors like business interruption, downtime, and extra expense, that ratio becomes more like 1:20. In terms of electrical fire exposure, depending on the size and type of facility, the average is 1:60. The savings can far exceed the investment.