
properties.trackTitle
properties.trackSubtitle
Sustainable construction doesn’t end when the building is complete, the building itself should have a reduced impact on the environment over its lifespan. This means that the building design should incorporate elements that have an ongoing positive influence on the building’s environmental impact. These can include proper insulation to prevent heat loss, solar panels to reduce energy consumption, and building materials with a long lifespan.
The construction industry accounts for an incredible 36% of worldwide energy usage and 40% of CO2 emissions. The manufacture of concrete has resulted in over 2.8bn tonnes of CO2, a figure which is only going to keep increasing as 4bn tonnes of concrete is poured every year.
Timber on the other hand is a natural and renewable building material, it has excellent ecological attributes, acting as a carbon sink with low embodied energy. The energy needed to convert trees into wood and hence into structural timber or panelised components is significantly lower than that required by other materials such as steel and concrete. Prefabricated material such as cross laminated timber (CLT), for example, works as a sustainable option due to its versatility and reduced weight1.
Here, at Munich Re, we are always looking at the ever-changing landscape of construction design and techniques that can help reduce the impact this industry has on the environment. One of which is modular construction. The construction industry often faces delays caused by numerous factors, including lack of labour, or weather conditions that halt or slow down construction onsite. Modular housing provides a solution to those problems. Building offsite within a controlled factory environment minimises risk, resulting in a faster build programme, assured quality control and enhanced building performance standards.
In fact, according to the UK’s Minister of State for Housing2, the industry shift to MMC is a global one with Tokyo capable of building more houses per year than the entire UK. This is simply because Japan has embraced sustainable construction for more than 50 years. The UK is currently seeing a huge uptick in MMC. Sweden is also leading the charge with approximately 45% of all new houses being built off-site in factories.
From increased energy efficiency to reduced build time, factory-built modular homes can be designed with occupants and the environment in mind. Yet, the method is not exclusive to the building of new homes. Munich Re recently provided a solution for a new special needs school in the UK that was completely fabricated in a local factory and the modular components brought to site and erected. This provided a complete turnkey solution for the client to deliver an energy efficient structure to the local education authority.
The utilisation of pre-manufacturing technologies brings construction into the modern age by transferring production to the factory. With greater quality control and more efficient use of labour and materials, particularly sustainable ones, and employing modern manufacturing techniques delivers a seamless product.
1) Modern Methods of Construction (RICS)
2) Modern Methods of Construction (Speech)
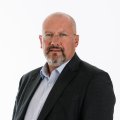