Digital Trends in Construction Industry
3.5 minutes read
Published: 03.07.2017
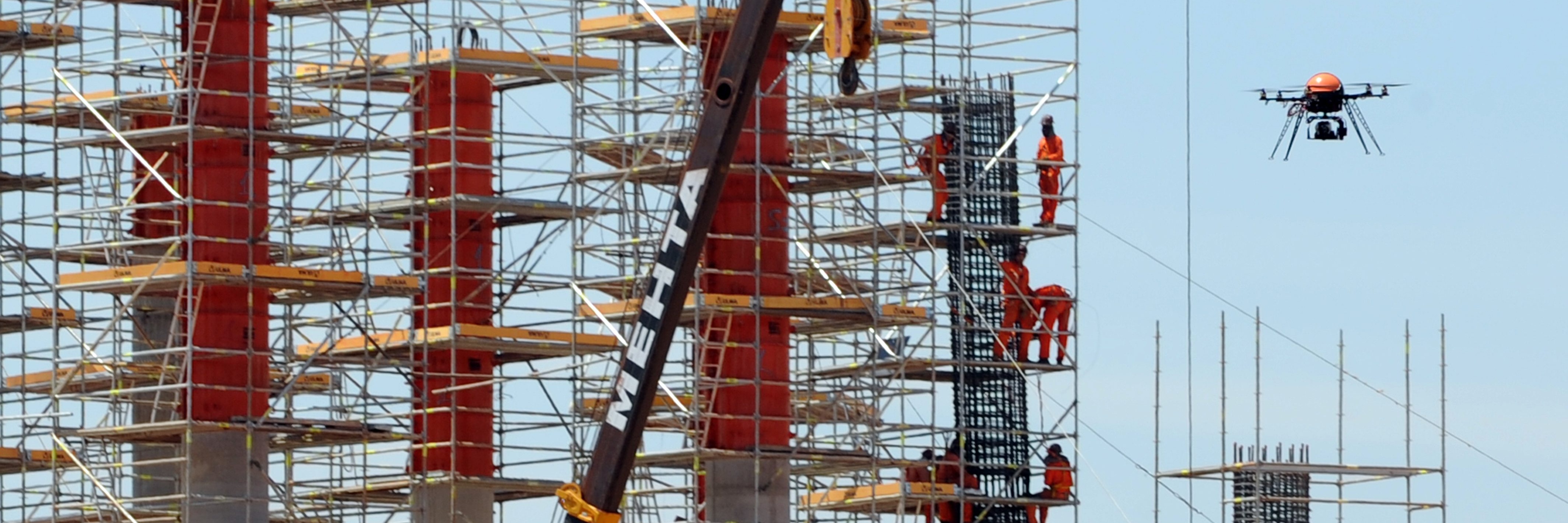
properties.trackTitle
properties.trackSubtitle
Delays, cost overruns, uncertain project planning and management – the construction industry is plagued by complexities. With digitalisation, contractors and project owners are able to draw on a growing array of innovative solutions to address these challenges. As promising as these new technologies are, will they really make construction and engineering easier?
Pressures in today’s construction industry include project delivery, lifecycle performance and sustainability, alongside the need to minimise costs. Motivated by long-term economic and ecological sustainability, increasing numbers of new “green” and “smart” buildings are being built. The novel solutions being developed for these buildings, like connected Internet of Things (IoT) sensors and wireless technologies, recycled or new and untested building materials, address many problems. But they also introduce new risks such as exposure to cyber attacks and inherent product defects or failure to meet performance requirements.
Economic conditions are changing
The future holds further challenges for the construction industry. There is uncertainty regarding the investment environment due to changing economic conditions, potentially leading to higher interest rates, or higher material costs caused by inflation. Another concern is a possible shortage of skilled workers due to aging demographics and an outflow from the workforce during a recession, putting pressure on the labour supply and driving up costs.
Digital tools for value chain of construction industry
Deployed intelligently, digital technologies have the potential to revolutionise construction. Although the industry is traditionally conservative and risk-averse, momentum in the adoption of digitalisation across all phases of the design and engineering, construction, operations and maintenance value chain is increasing. Solutions already in use to improve project planning and management include enhanced IT software tools such as building information modelling (BIM), virtual/augmented reality (VR/AR), 3D imaging, light detection and ranging (Lidar) technology, digitalised project management workflows using the Global Positioning System (GPS) and Radio Frequency Identification (RFID), drones, robotics and autonomous vehicles. In addition, 3D-printed materials, embedded sensors and advanced analytics are increasingly integrated into buildings.
Analytics tools improve project management
In practice, this means precise data from Lidar 3D laser scanning, for example, can be used with integration of 3D computer software to compare current conditions at a construction site against a virtual model. This enables project managers to detect even the smallest errors before they create problems, decreasing rework and avoiding downtime. Drones are used to capture 3D images and photos to improve workflow visibility and to check for construction violations and security, improving workplace safety and reducing fraud. With advanced analytics, data from embedded sensors can be used to optimise inventory levels and flows, reduce downtime and cut costs via preventive maintenance and remote monitoring.
Drones, robotics and sensors reduce risks
From an insurance perspective, imagery in real time from drones can provide better and more accurate loss estimation and claims handling. Prefabricated customised building materials produced using 3D printing or additive manufacturing can save time and labour costs while cutting waste. Using robots for heavy work like demolition, laying bricks and concrete or arc welding on structural steel reduces the risk of workplace injury, while at the same time enhancing efficiency and quality. Wearable devices with smart sensors can monitor a worker’s physical condition. Glasses equipped with cameras can record, transmit and analyse information on the worksite, increasing both safety and efficiency.
Data and analytics tools are most relevant for success
As compelling as the advantages of digitalisation are, adoption in the construction industry is slow. For example, usage of robotics and automated systems, technologies with well-established effectiveness in other industries like manufacturing, remains at around 30 percent according to the recent study Global-Construction-Survey 2016 of global audit, tax and advisory service provider KPMG. But inaction is not an alternative: in terms of business viability, sustainability and risk management, the future belongs to those who embrace digitalisation. The study by KPMG identified data and analytics as a key success factor in the future of construction. While the findings also point to the need for excellence in the traditional disciplines of construction and the human factor, it stresses the urgency of a sound technology strategy. For the construction industry, the message is clear: adopt digital technologies early and wholeheartedly as solutions for the biggest problems you face – complexity and inconsistency in costs, quality and completion times.
Related Topics
Newsletter
Stay ahead of the curve with exclusive insights and industry updates! Subscribe to our Munich Re Insights Newsletter for a front-row seat to the latest trends in risk management, expert analyses and assessments, market insights, and innovations in the insurance industry. Join our community of forward-thinkers at Munich Re and empower your journey towards a more resilient future.