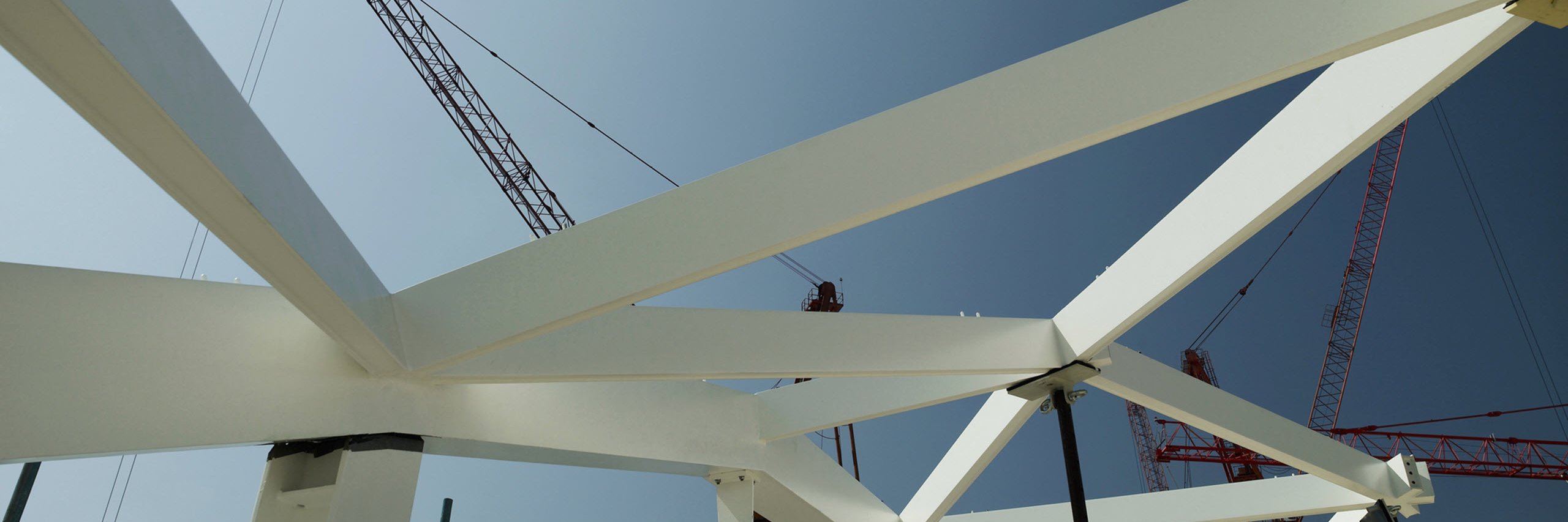
The management of temporary works in the construction industry
A guide to loss prevention
properties.trackTitle
properties.trackSubtitle
What Construction Site Managers need to know when installing temporary works for permanent basement and underpinning works
Construction Design and Management (CDM) 2015
All construction projects must operate in line with CDM 2015 regulations (replacing CDM 2007). The regulations provide clear instruction on how construction projects must be run and what criteria makes a project notifiable. The regulations are bound in law and impositions can be imposed for breaching the regulations in the form of fines and prison sentences.
The regulations provide a clear understanding of the roles and responsibilities of each stakeholder and form a guide as to how temporary works must be managed to ensure the safe execution of high risk works including basement and underpinning works.
Projects with high risk works will be compliant with CDM 2015 if the following is provided:
- A TWC or TWS is formerly appointed (for high risk works)
- There is a design brief
- There is a temporary works register
- There is a coherent design of both the temporary and permanent works which has been checked in accordance with BS 5975
Management of temporary works
The correct design and execution of temporary works is an essential element of risk prevention and mitigation in construction. BS 5975 provides recommendations and guidance on the procedural controls to be applied to all aspects of temporary works in the construction industry and on the design, specification, construction, use and dismantling of falsework.
Examples of temporary works include, but are not limited to:
- Earthworks - trenches, excavations, temporary slopes and stockpiles.
- Structures - formwork, falsework, propping, façade retention, needling, shoring, edge protection, scaffolding, temporary bridges, site hoarding and signage, site fencing, cofferdams.
- Equipment/plant foundations - tower crane bases, supports, anchors and ties for construction hoists and Mast Climbing Work Platforms (MCWPs), groundworks to provide suitable locations for plant erection, e.g. mobile cranes and piling rigs.
Temporary Works Coordinator (TWC) and Temporary Works Supervisor (TWS)
The TWC and TWS must be formerly appointed by either the client or the contractor and either may carry out the role of Principal Designer, however, a Suitably Qualified and Experienced Person (SQEP) is generally nominated to do so.
Temporary Works Coordinator (TWC)
The TWC is responsible for ensuring that the contractor’s procedures for the control of temporary works are implemented on site. The TWC is not normally the designer, but is responsible for ensuring that a suitable temporary works design is prepared, checked and implemented on site in accordance with the relevant drawings and specification.
The TWC for a project should be formally appointed and have adequate authority to carry out their tasks, including stopping the work if it is not satisfactory. It is essential that those selected are competent, have completed formal TWC training which they are up-to-date with, and have experience of the relevant types of temporary works. A Chartered Civil or Structural Engineering qualification is desirable.
Temporary Works Supervisor (TWS)
On larger sites, or where a number of subcontractors are involved, it may be appropriate for one or more Temporary Works Supervisors (TWS) to be appointed. A TWS should report to the TWC and assist them in the supervision of temporary works.
Temporary works procedure
Contractors should be able to demonstrate that they have effective arrangements in place for controlling risks arising from the use of temporary works. These are usually captured in a temporary works procedure which will contain most or all of the following elements:
- Appointment of a Temporary Works Coordinator (TWC)
- Preparation of an adequate design brief.
- Completion and maintenance of a temporary works register.
- Production of a temporary works design (including a design risk assessment and a designer’s method statement where appropriate).
- Independent checking of the temporary works design.
- Issue of a design check certificate, if appropriate.
- Pre-erection inspection of the temporary works materials and components.
Control and supervision of the erection, safe use, maintenance and dismantling of the temporary works should be carried out in line with the below procedures:
- Checking that the temporary works have been erected in accordance with the design, and issue a formal 'permit to load' where necessary.
- Confirming when the permanent works have attained adequate strength to allow dismantling of the temporary works, and issuing a formal 'permit to dismantle' where necessary.
- Including measures to ensure that the design function and role of the TWC and TWS's (where appropriate) are carried out by competent individuals.
Smaller contractors may not have the experience to operate their own temporary works procedure and may need to obtain external expertise. It is also common for large and medium contractors to outsource aspects of temporary works design and management.
The principal activities of the TWC are listed in clause 7.2.5 of BS5975:2008. On some projects, particularly smaller jobs involving lower risk temporary works, it may be appropriate for the TWC and designer roles to be carried out by the same person, provided that they are competent to carry out each of the roles.