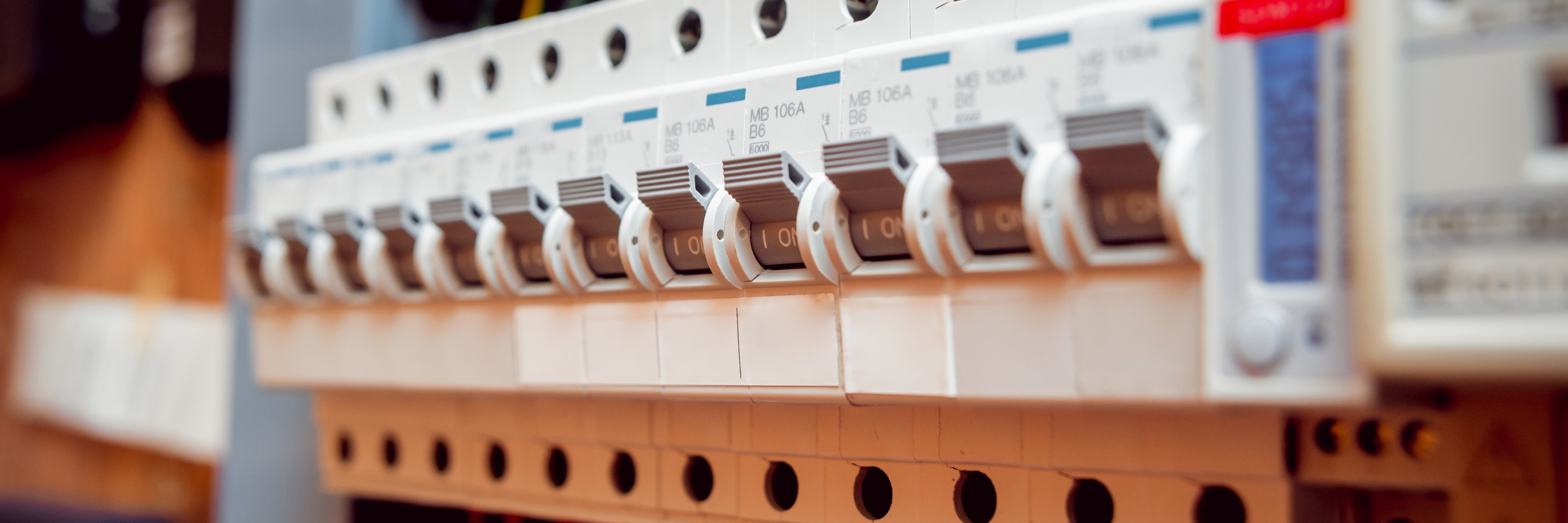
Property owners’ electrical installations
Top five self-checks between formal inspections
properties.trackTitle
properties.trackSubtitle
Properties can contain an ever-growing amount of electrical equipment; from televisions to tablets, and LED bulbs to (often numerous) plug-in chargers
Over a 12-month period during 2019/20, there were more than 25,000 accidental property fires in England. With almost 34% of those fires caused by electrical faults/misuse(1), electrical hazards can pose a major threat to the general public; and with the variety of non-compliant electrical switch gear and appliances available to purchase online, it’s easy to see how electrical fires can happen.
How can property owners reduce the electrical risks in their properties?
UK
The UK Health & Safety Executive defines a 'Competent Person' as "someone who has the necessary skills, experience and knowledge to manage health and safety".
Depending on the particular legislation, the Competent Person can be either an individual or the body which employs the individual to provide inspection services.
Ireland
Formal inspections must be conducted by a Competent Person at the frequency specified in the Wiring Regulations (in BS7671, this is commonly every five years for commercial property and three years for industrial properties). Observations in electrical inspection condition reports should be acted upon and kept on file along with electrical repair, maintenance and warrantee documents. Should an adverse electrical event occur, evidence will need to be provided to show how and when the electrical installation was maintained.
Whilst the Competent Person conducts periodic inspection and testing to identify any hidden dangers and deterioration affecting the installation, alterations and damage may occur between the required inspection periods. This is why it is important that property owners know what to look for and how to tell if electrical systems are unsafe.
Top five visual self-checks
1. Check the intake position
This is where the supply authority connects to the meter and the main switchgear in the premises.
- Remove all stored equipment (spare paint, aerosols, boiler suits, coats and other flammable goods) from around or near the switchgear.
- Make sure a suitable fire extinguisher (typically CO2) is easily accessible and stored in close proximity.
- Make sure a suitable rubber floor mat is in front of the main switchgear.
- Ensure all isolation points are labelled, voltage warning labels are fitted and there is a label on the doorway.
- Make sure the switchroom door is kept locked, labelled and only accessible to skilled or instructed persons.
2. Check the distribution boards
These are the enclosures throughout the building that contain the protective devices (i.e. fuses, MCBs and RCDs).
- Clear any stored equipment from around or on top of distribution boards.
- Fit insulated blanking pieces to external holes and unused fuseways, and make sure the enclosures are undamaged and securely fitted.
- Ensure enclosures are labelled with a unique number/name and detail of their supply point.
- Ensure the circuit legend is fitted inside or near each distribution board and kept up to date as this will speed up any urgently-required isolations.
- Press the RCD test buttons every six months.
3. Check the condition of accessories
These include light switches, sockets, spur units and local isolation switches.
- Check that lights and switches are not flickering or buzzing as loose or broken wiring is a common cause of fire.
- Do not use socket outlets, spur units or lights that show signs of damage, and replace any missing fixing screws.
- Make it common practice to ensure socket outlets are switched off before plugging appliances in. High current appliances (e.g. kettles) can damage sockets, so check for signs of arcing or overheating.
- Never overload sockets. Remove any socket adaptors as they can become overloaded in your absence.
- Extension leads should only be used temporarily. Ensure they are in good condition and not hidden (such as under carpet) or used in areas susceptible to damage.
4. Check all appliances
Portable and fixed electrical equipment.
- Make it a habit to turn off appliances when they are not in use.
- Never allow cables to trail over kitchen appliances (e.g. toasters or hobs). Make sure long leads and IEC leads (e.g. kettle leads) cannot come into contact with water or conductive parts.
- Make sure appliances carry a CE mark, they are undamaged (including the cable and plug) and the correct rating of fuse is fitted.
- Make it a common practice to unplug and visually check the plug, lead and the appliance itself before use.
- Create a register of the portable appliances you provide at the property, and keep a record of testing (also known as PAT testing), repairs and maintenance.
5. Check any alterations
- Any major alterations to fixed wiring needs a formal inspection and condition report by a Competent Person.
- Use a reputable contractor for repairs to your wiring installation.
- If you are having a new circuit fitted, ensure the contractor connects correctly to the supply. It is common for contractors to incorrectly connect the supply to a used MCB/fuse because there is no space in the distribution board to fit a new one. It is acceptable to add a junction box to an existing circuit away from the distribution board, but never an uninsulated connector block.
- Any person fixing something to the wall, excavating indoors/outdoors or working in your roof space runs the risk of damaging the fixed wiring cables, so ensure they are aware of where cables are before they begin work and check them after they have finished their work.
- Think about your wiring when you have alterations to other service areas. Keep cables clear of loft insulation and do not route water pipes near the electrical system.
HSB Inspection Services
(2) The context of this document assumes a typical property with a single or three-phase supply and distribution boards.