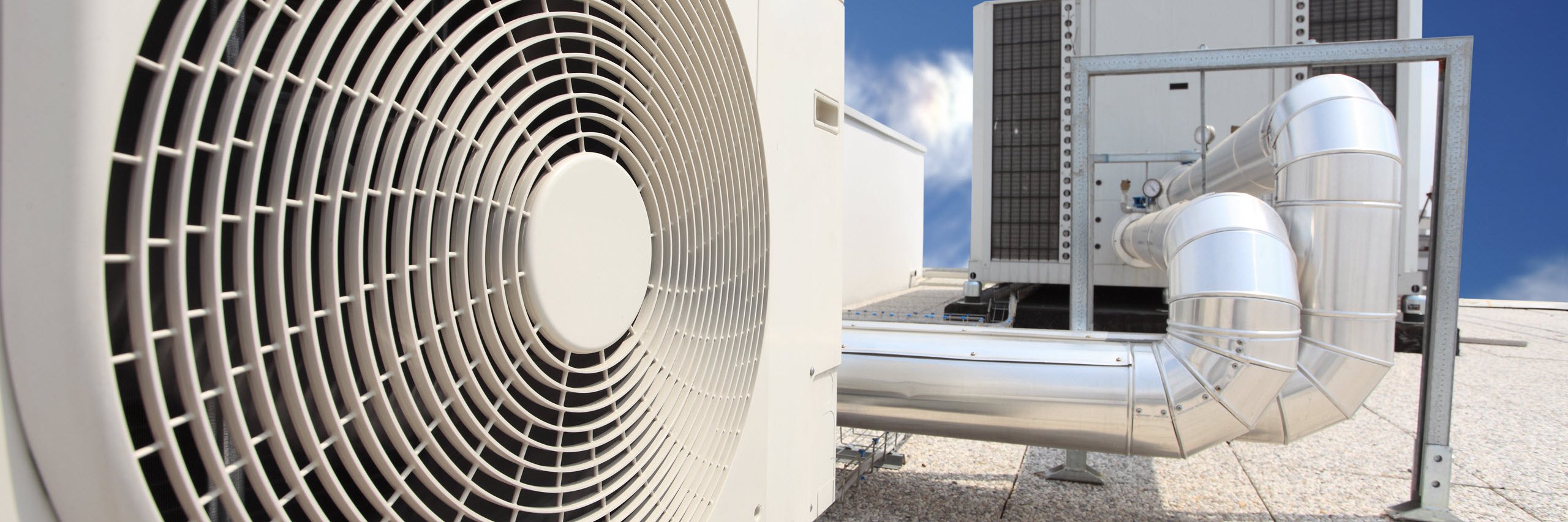
How to make sure your air conditioning keeps its cool
properties.trackTitle
properties.trackSubtitle
If you’re going to have an air conditioning failure, it’s going to occur during early summer; when most air conditioning breakdowns materialise
That’s why we’re offering tips from our engineers on how to avoid the most common air conditioning problems with a little strategic maintenance.
The section numbering of this guide directly relate to the references shown on the three diagrams.
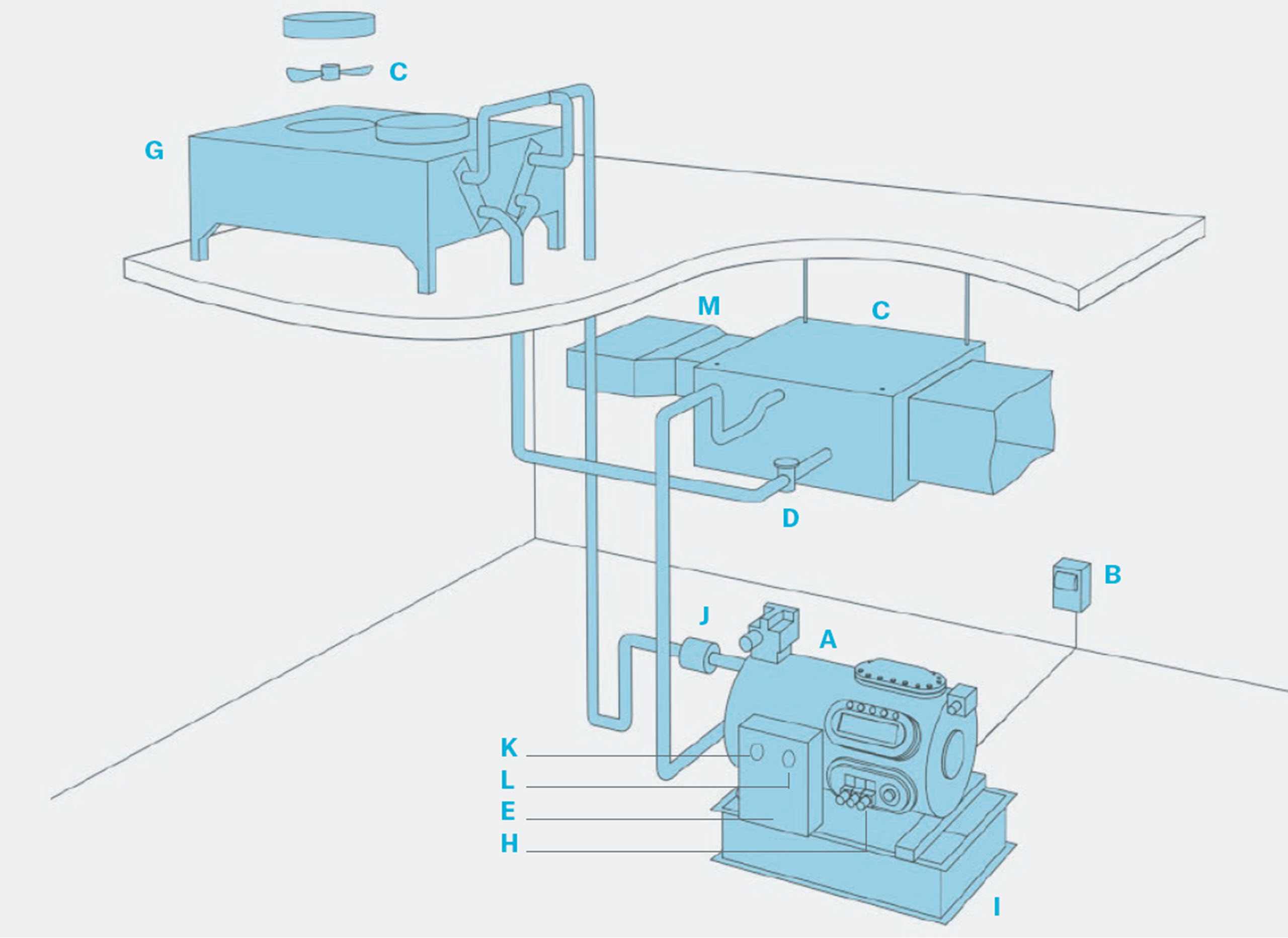
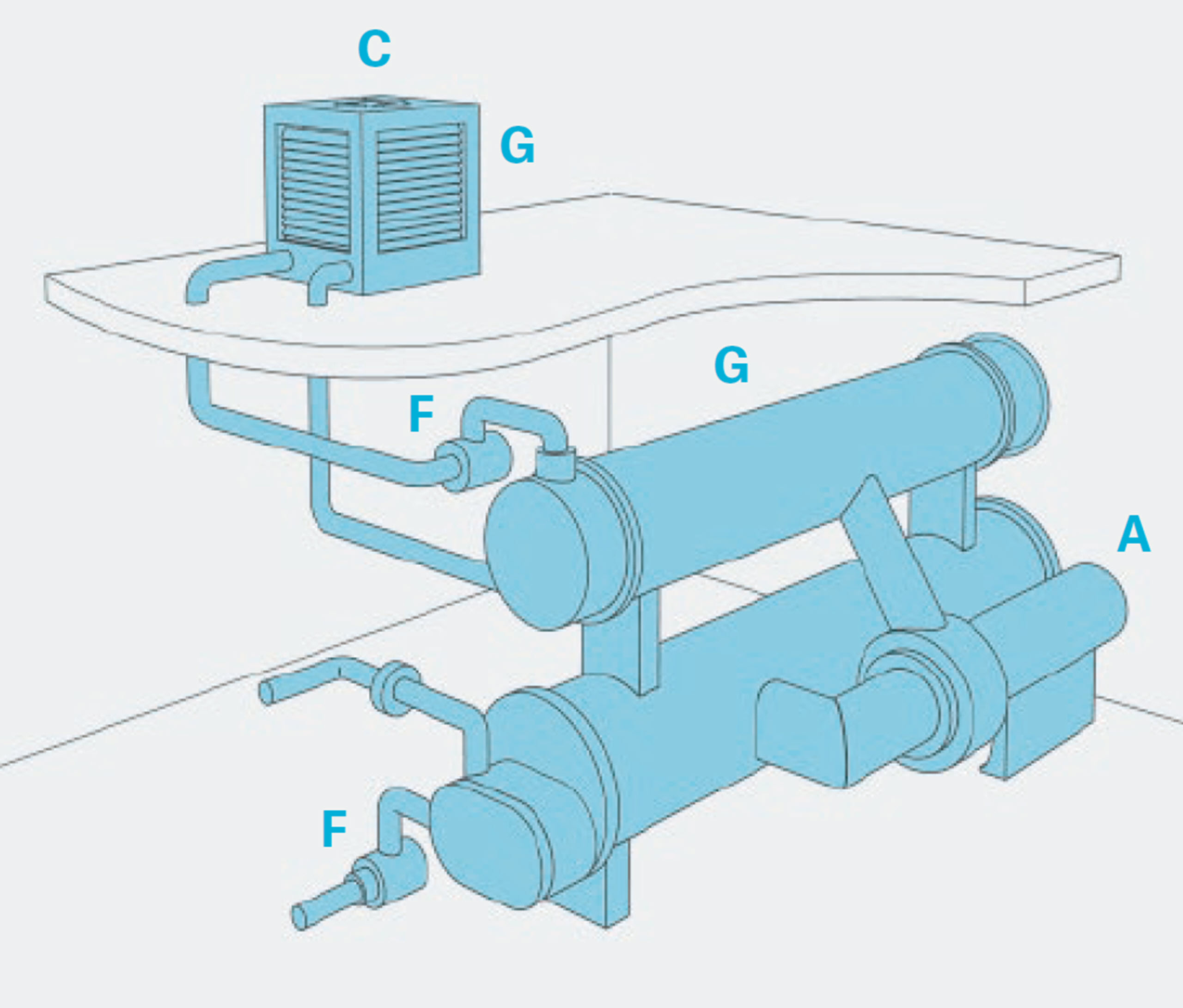
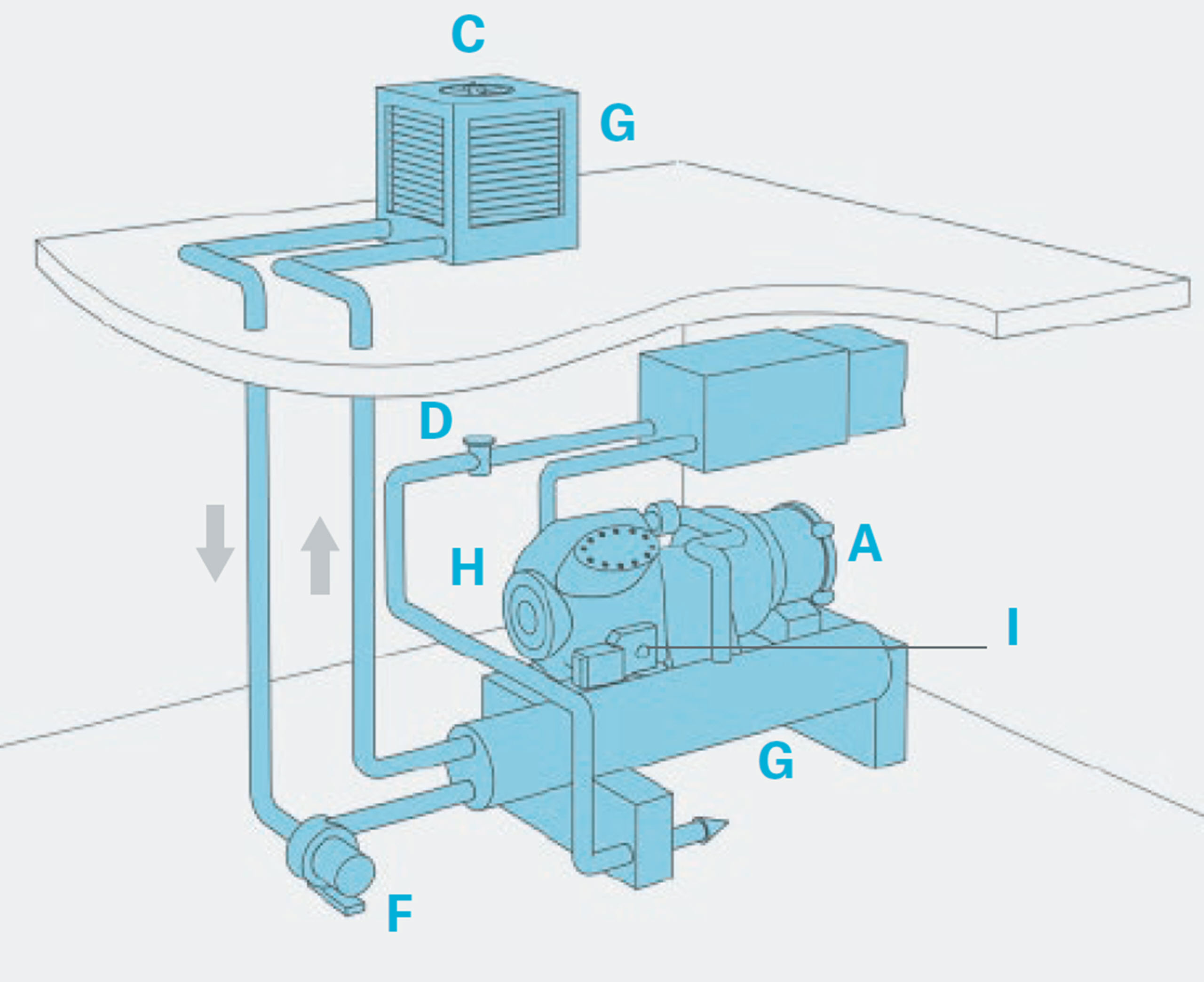
A. Annually check open or hermetic motors for burnout
- Check air ventilation openings on open-type motors for obstruction.
- Check bearings on open-type motors for adequate and proper lubrication.
- Have insulation resistance meter readings taken on motor windings. If resistance is less than one megohm, don’t start the motor. (For hermetic motors, be sure the crank case heater is energised at least eight hours before this test.)
B. Annually inspect motor controls
- Remove the covers on the motor’s magnetic starters and examine the contacts. Compressor cycling can make them deteriorate. Look for pitting or corrosion.
- Check all terminal connections for tightness.
- Check the overload protection for defects and proper sizing.
- Make sure timing devices have the correct operating sequence.
- Check mechanical linkage for binding and looseness.
C. Monthly check the fans
- Check fans for broken, cracked, bent or loose blades and hubs.
- Check the fan shaft and bearings.
- Check belt tension and condition.
D. Annually check the thermostatic expansion valve
- Check it for proper superheat setting over its full range of operation. If it's not operating within its design limits, it can affect the safe operation of the equipment.
E. Annually check the operating and safety controls
- They're the heart of your equipment. Make sure they're properly calibrated and in working order.
- Immerse thermal sensing controls in a cold medium to verify the condition and setting of their sensing elements.
- Test oil pressure differential switches mechanically and electrically. Flow switches should be removed from the well for examination. Be sure to look for signs of corrosion on the paddle and linkage.
F. Monthly check the pumps
- Check the condition of pump bearings, packings, shaft couplings and seals.
G. Annually clean the condensers/cooling towers
- Clean air-cooled condensers, but only with a solution marketed for this specific use. Take care to protect the fan motors from any moisture.
- Remove the heads on shell and tube condensers and clean the tubes of scale and debris.
- Clean the coils, sump, spray nozzles and overflow drain on evaporative condensers.
- For cooling towers, clean the sump and spray nozzles and check the baffles for tightness and soundness.
- Check the makeup water valve to be sure it’s operating properly.
H. Help prevent ‘scrambled’ compressors
- At least eight hours before start-up, hermetic compressors need to have their crank case heater energised.
- This step is vital: preferably, leave the heaters energised for the rest of the season; when the compressor is idle, the heater will prevent refrigerant from migrating to the compressor.
- Have the cylinder heads removed and check the compressor valves at least once every two years, or every 10,000 hours. Valve failure is one of the biggest causes of compressor breakdown. If you see signs of wear or fatigue, replace them (valves are relatively inexpensive).
Avoid lubrication failure
Lubrication failure is one of the biggest causes of equipment breakdown. Without proper lubrication at all times, moving parts in the motor-compressor wear out, overheat, burn and break.
Every year, have your service technician check the oil to make sure it’s suitable; clean and non-acid.
Also have the technician leak test the system regularly, and repair any point of leakage immediately.
I. Weekly check lubrication
When the system is idle, look through the oil sight glass to check lubrication in the compressor crankcase. The oil level should remain constant. If you temporarily lose oil in the sight glass, you may have unwanted refrigerant in the crankcase. Call the service technician at once.
Oil and refrigerant leaks often show up as oil spots with dust accumulations – a symptom of trouble.
Check these likely leak spots every week: compressor shaft seals • piping joints • coils • vessels • compressors • motors.
J. Avoid refrigerant circuit failure
Moisture hurts any refrigeration system; preventing proper lubrication, corroding or copper plating the moving parts, and freezing in the expansion valves. The result: erratic performance, inefficiency, and even breakdown.
Moisture can enter the system if water-cooled condensers or water chillers leak. It can get in accidentally when you’re charging refrigerant or oil into the system, unless you take special care. Here’s how to check for moisture problems:
- Equip your refrigerant circuit (liquid line) with a moisture sight glass indicator. Look for any change in the indicator chemical colour. If the colour changes toward ‘wet’, make sure your service technician corrects the problem, cleans and dries the system, and installs proper liquid and suction line filters and dryers.
- It’s even more important to determine the source of the moisture and to correct it right away. You may need to leak test any water-cooled condensers or chillers.
- Normally, you’ll see a pattern of clear liquid flow. If you notice other changes in the flow pattern (such as gas bubbles in the liquid refrigerant), have the system checked to see if it’s properly charged with refrigerant. Control malfunction can also cause flow pattern changes.
K. & L. Regularly check temperature (K) and pressure (L) controls
Effective air conditioning depends on reliable temperature and pressure controls. Each is calibrated to perform a specific function. Periodically, have them serviced, adjusted and prooftested; and only by qualified personnel.
When your system shuts down, check these areas
Above-normal room temperatures invariably spell trouble. If there hasn’t been a power interruption and all other checkpoints appear normal, call the service technician.
If the motor-compressor has shut down, don’t attempt to restart the system
Protective controls may have tripped it off; find and correct the cause of the trip-off. Don’t attempt to restart the system – it could result in severe equipment breakdown.
Don’t attempt to adjust regulating or protective controls yourself
This is the time for an expert to diagnose and correct the problem.
Avoid pressure problems
Try to determine normal discharge and suction pressures (your air conditioning unit may be equipped with pressure gauges). As with temperature changes, any increase in pressure is reason enough to call the service technician at once.
Dirty condensers are a key cause of pressure and temperature problems. Make sure the technician verifies that the condenser is clean. If you have a water-cooled or evaporate condenser, use an effective water treatment to prevent scale, corrosion and algae.
M. Keep air filters clean
- Keep air filters free of dust particles, smoke and dirt. Keep a careful log of cleaning dates to maintain an effective cleaning schedule.
Absorption unit systems1
Evaluate the lithium bromide solution concentration and the lithium bromide inhibitor.
Check the absorption purge unit and purge system for proper operation.
Examine all canned motor pumps used on the absorber unit and check the bearings for wear. Look carefully at the condition of the motor stator and rotor seals.
Our diagrams can help you work with service people to identify parts needing replacement, points of refrigerant leakage, with regulating and protective control settings, and other critical features.
Insulation
Insulation should be checked for breakdown of the vapour barrier. This could be due to external damage or the insulation deteriorating. The failure of the insulation is usually indicated by condensation or frosting on the surface. In such cases, the insulation should be remove and the pipework inspected for any surface corrosion and be protected as necessary, prior to reinsulating.
If operating characteristics change, watch out
Each system has its own normal pattern of noise, vibration, speed, temperature and pressure. They can vary depending on the season and the heat load your system handles. Once you've familiarised yourself with these normal conditions, you’ll be able to spot trouble signs.
Any change in normal operating characteristics is a warning. Call the service technician if you notice:
- an unusual noise or vibration
- a strange odour
- oil or water spots
- sudden changes in temperature, speed or pressure.
Correct the problem at once.
Suspect a problem? Call your service firm.
That’s critical advice. Consult with a professional before undertaking any maintenance steps or repairs. An adequate service programme may cost a little more up front, but it will pay off in long-term savings.