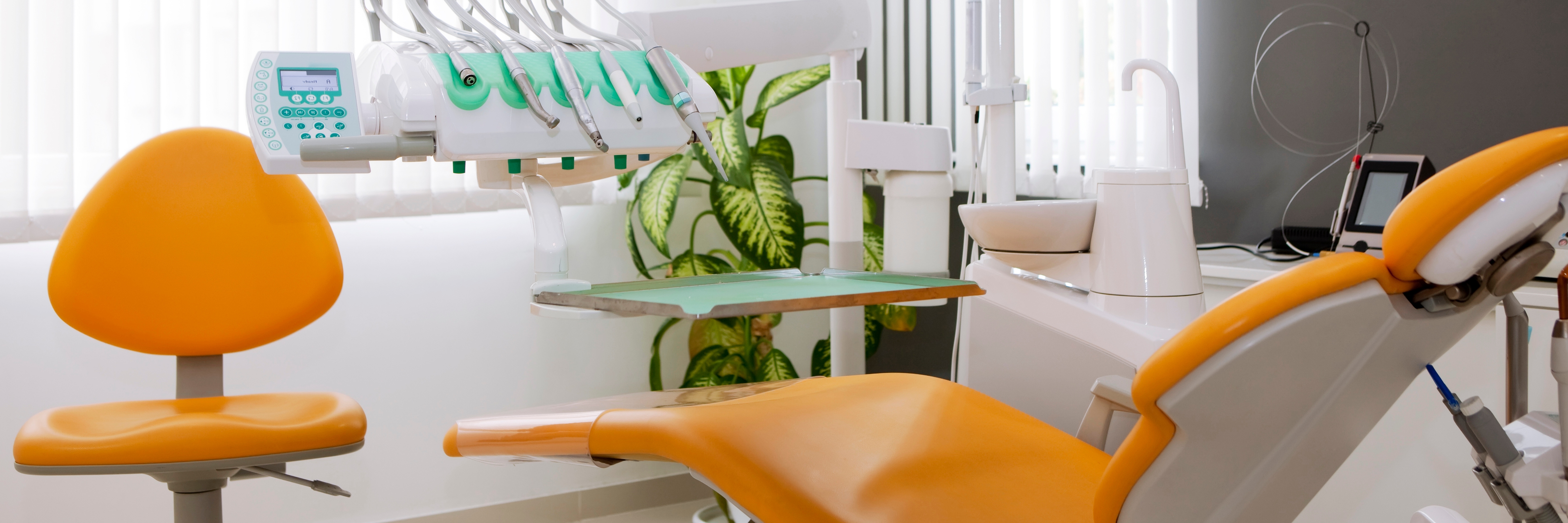
Healthcare: Doctors, dentists and veterinary surgeries
A guide to inspection frequencies
properties.trackTitle
properties.trackSubtitle
Employers have a duty of care to ensure the health, safety and welfare of their employees. Periodic inspections and/or thorough examinations on their plant and equipment form part of this vital duty, whilst also ensuring employer conformity to applicable health and safety legislation.
Plant and equipment within the workplace needs to be examined and properly maintained to ensure it is safe to operate, and that it complies with applicable health and safety legislation; requiring statutory examinations at specific intervals, which exist outside normal equipment maintenance and servicing procedures.
Regular inspections may also serve as a good preventative maintenance programme to ensure the integrity of plant and equipment; helping to minimise machinery breakdowns and production downtime.
Inspection frequencies
Different types and categories of equipment have varying inspection frequencies according to applicable health and safety legislation.
Typical equipment and installations found within doctors, dentists and veterinary surgeries are listed below, together with the applicable legislation.
UK
Lifting
Applicable legislation (1) | Typical equipment | Inspection frequency (months) |
---|---|---|
Lifting Operations and Lifting Equipment Regulations 1998 | Passenger lift | 6 |
Boiler/Pressure
Applicable legislation (1) | Typical equipment | Inspection frequency (months) (2) |
---|---|---|
Pressure System Safety Regulations 2000 | Autoclave/steam steriliser | 14 |
Air receiver (>250 bar/litres) | 26 | |
Provision and Use of Work Equipment Regulations 1998 | Refrigeration and air conditioning systems (<25 kW) (3) | 12 |
Hot water boiler (<110ºC) (3) | 12 | |
Expansion vessel (used for hot water systems) | 12 |
Electrical/Mechanical Plant
Applicable legislation (1) | Typical equipment | Inspection frequency (months) |
---|---|---|
Provision and Use of Work Equipment Regulations 1998 | Alternator | 12 |
Local Exhaust Ventilation
Applicable legislation (1) | Typical equipment | Inspection frequency (months) |
---|---|---|
The Control of Substances Hazardous to Health Regulations 2002 | Fume extraction | 14 |
Dust extraction (metallic: dentistry) | 6/14 (2) | |
Dust extraction (non-metallic) | 14 |
Electrical Systems
Applicable legislation (1) | Typical equipment | Inspection frequency (months) (2) |
---|---|---|
Electricity at Work Regulations 1989 | Low voltage electrical installations: medical clinical areas | 12 |
Low voltage electrical installations: general areas | 60 | |
Portable appliances | 12 |
Ireland
Lifting
Applicable legislation | Typical equipment | Inspection frequency (months) |
---|---|---|
S.I. No. 299 of 2007: Safety, Health and Welfare at Work (General Application) Regulations 2007 | Passenger lift | 6 |
Boiler/Pressure
Applicable legislation | Typical equipment | Inspection frequency (months) |
---|---|---|
S.I. No. 445 of 2012: Safety, Health and Welfare at Work (General Application) (Amendment) Regulations 2012 | Autoclave/steam steriliser | 14 |
Air receiver (>250 bar/litres) | 26 | |
S.I. No. 299 of 2007 (Regulation 30): Safety, Health and Welfare at Work (General Application) Regulations 2007 | Refrigeration and air conditioning systems (<25 kW) | 12 |
Hot water boiler (<110ºC) | 12 | |
Expansion vessel (used for hot water systems) | 12 |
Electrical/Mechanical Plant
Applicable legislation | Typical equipment | Inspection frequency (months) |
---|---|---|
S.I. No. 299 of 2007 (Regulation 30): Safety, Health and Welfare at Work (General Application) Regulations 2007 | Alternator | 12 |
Local Exhaust Ventilation
Applicable legislation | Typical equipment | Inspection frequency (months) (1) |
---|---|---|
Health & Safety Authority: Local Exhaust Ventilation (LEV) Guidance document | Fume extraction | 12 |
Dust extraction (metallic: dentistry) | 12 | |
Dust extraction (non-metallic) | 12 |
Electrical Systems
Applicable legislation | Typical equipment | Inspection frequency (months) |
---|---|---|
S.I. No. 299 of 2007 (Part 3): Safety, Health and Welfare at Work (General Application) Regulations 2007 | Low voltage electrical installations: medical clinical areas | 60 - Hospitals (1) |
12 - Operating theatres (1) | ||
Low voltage electrical installations: general areas | 12-60 (1) | |
Portable appliances | 3-60 (2) |
How HSB can help
HSB Inspection Services: Our network of competent, multi-skilled Engineer Surveyors help customers throughout the UK and Ireland to maintain workplace equipment safety, optimise the efficiency of plant and equipment, and comply with applicable health and safety legislation; covering boiler/pressure, lifting, electrical/mechanical, dust and fume extraction, power press equipment, and fixed wiring installations.
HSB Risk Management Solutions: We can help businesses to reduce risks, costs, and deliver compliance via improved analysis of their equipment and health and safety practices. Consisting of three services, each service is further split into modules, allowing customers to build them to fit their business.