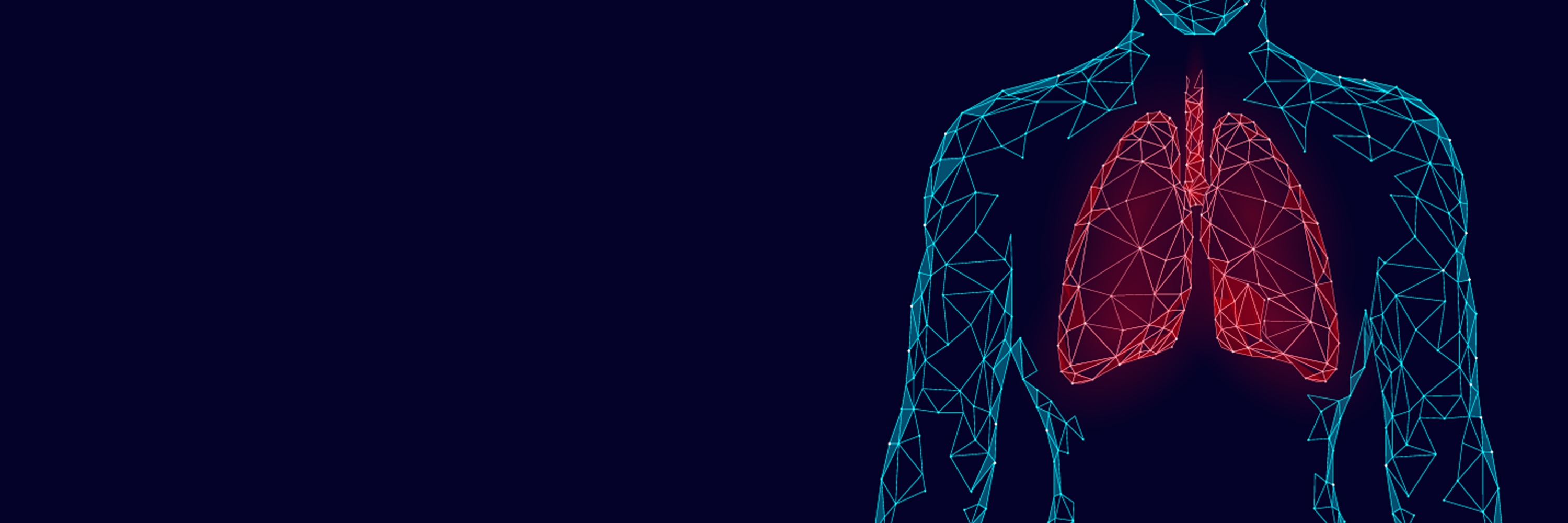
Give a Breath – Challenge
an initiative by Munich Re and Fraunhofer
properties.trackTitle
properties.trackSubtitle

In the face of the corona pandemic, Munich Re and Fraunhofer-Gesellschaft have launched a challenge with the aim of pooling the most capable minds with a brief to alleviate the consequences for those severely affected all around the world.
In March the Give a Breath Challenge set out to identify the best designs and blueprints to enable the immediate and decentralised production of emergency ventilation equipment.
The challenge was equipped with a budget of more than €1 million for prize purses and a realisation fund. We received many excellent ideas and seven teams made it into the shortlist to refine and finalize their designs.
The winners’ equipment: versatile, inexpensive, multi-purpose
Over 150 project designs were submitted worldwide. Seven teams were selected for the final in April and received support for the manufacture of prototypes. In mid-July, the prototypes were examined by experts at the ETH Zürich (Swiss Federal Institute of Technology Zurich) and Prof. Dr. Dieter Köhler, former president of the German Society for Pneumology (DGP), who applied internationally recognised testing methodologies. The jury determined the winners on the basis of their findings.
From now on the way is paved for 3D-manufacturing on site for the best designs to combat the consequences of an COVID-19 infection. A pilot will be kicked off in South Africa together with the Stellenbosch University among others.
And the winners are…
Challenge I: first prize – SmartCPAP
The SmartCPAP team together with AC Aircontrols GmbH developed a non-invasive ventilator that can be produced inexpensively anywhere and used in a wide range of conditions. The machine has some special features that make it particularly suitable for Covid-19 patients. For example, it assists patients very flexibly and spontaneously with breathing both in and out, thereby providing support for as long as possible without intubation so that intensive-care beds can be kept free for more serious cases. The SmartCPAP can work with oxygen from various different sources and also has features that save oxygen – an important aspect in a crisis in which oxygen is a rare commodity.
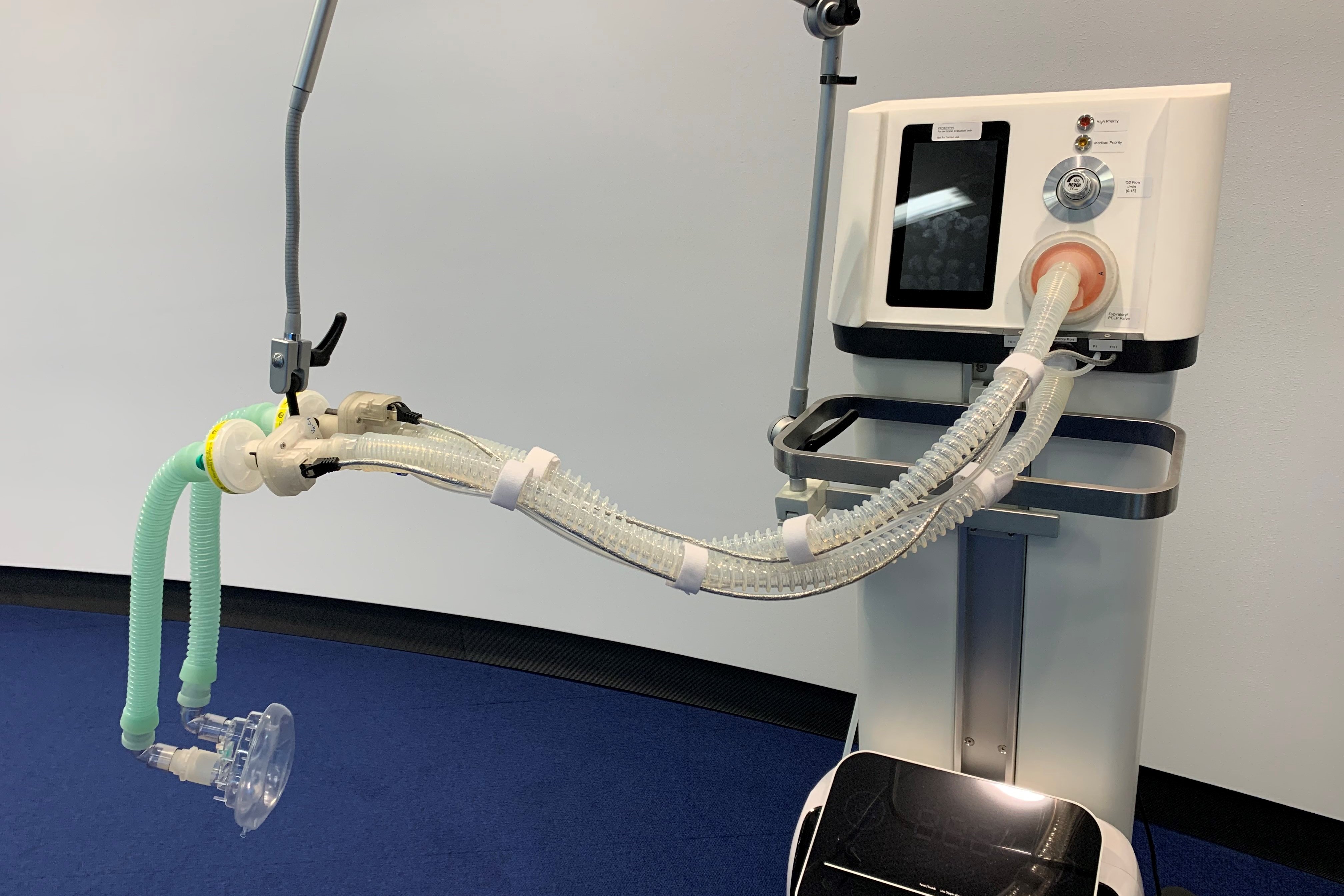
Challenge I: first prize – Vivid Breath
The Vivid Breath team also received an award in this category. Vivid Breath developed an exceptionally inexpensive respirator system comprising an O2 concentrator and a ventilator. It offers various possibilities for ventilation and other purposes in addition to its current use for Covid-19 patients. The O2 concentrator can supply up to six patients with oxygen at the same time. The materials and components required can be procured easily or manufactured locally using a 3D printer.
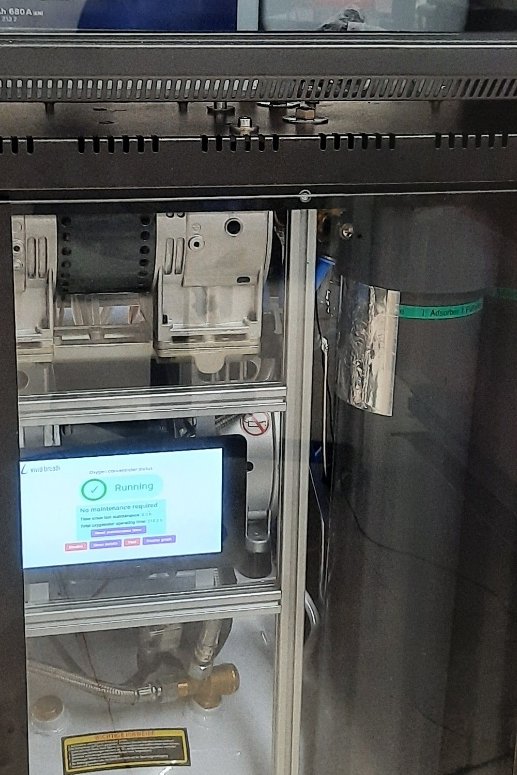
Challenge II: first prize – Soteria
The Soteria team was the winner in the respiratory mask category. A 3D printer is also all that is needed to produce a Soteria mask. Due to its innovative internal honeycomb structure, it can be adapted flexibly to different shapes and sizes of face, enabling it to be sealed very effectively. It can also be used for many different types of ventilator. Assembly instructions with illustrations and a video tutorial help ensure that it can be quickly introduced.
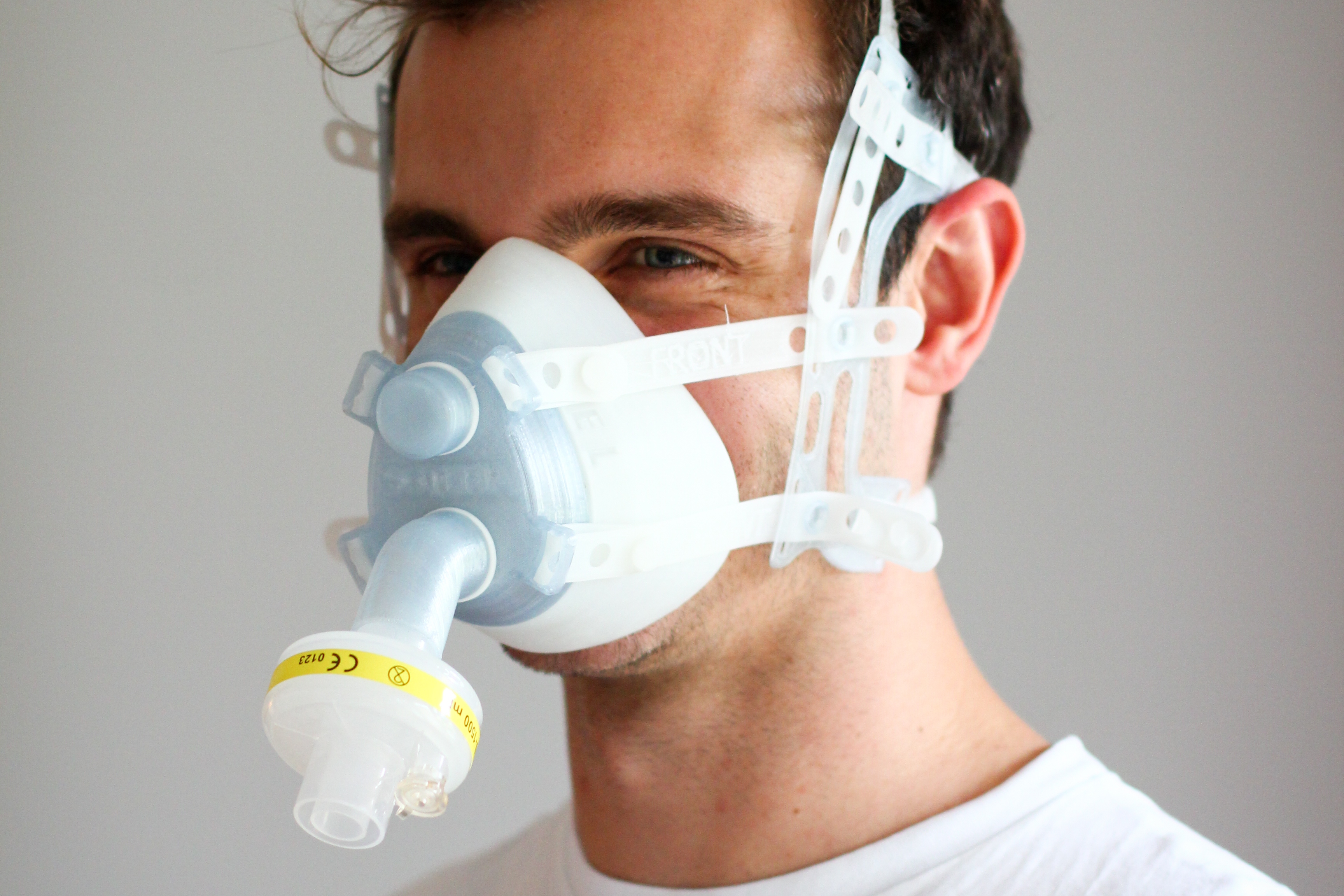
Challenge III: first prize – Virus Fighter´s Handbook
The Virus Fighter’s Handbook was the winner in the training material category. A team from the Project Group for Automation in Medicine and Biotechnology (PAMB) at the Fraunhofer Institute for Manufacturing, Engineering and Automation (IPA) worked with experts from Festo SE & Co. KG and doctors from a number of clinics to develop the design of a digital manual based on an existing app. Registered users receive information via the app on the use and maintenance of the newly developed equipment, with specific information provided on treating Covid-19 patients.
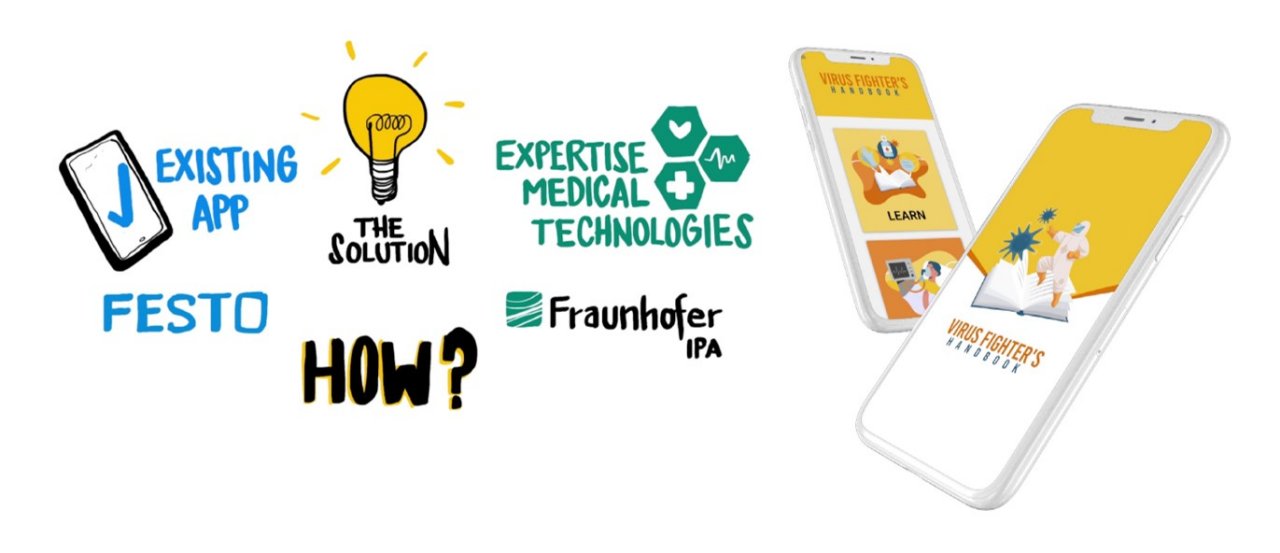
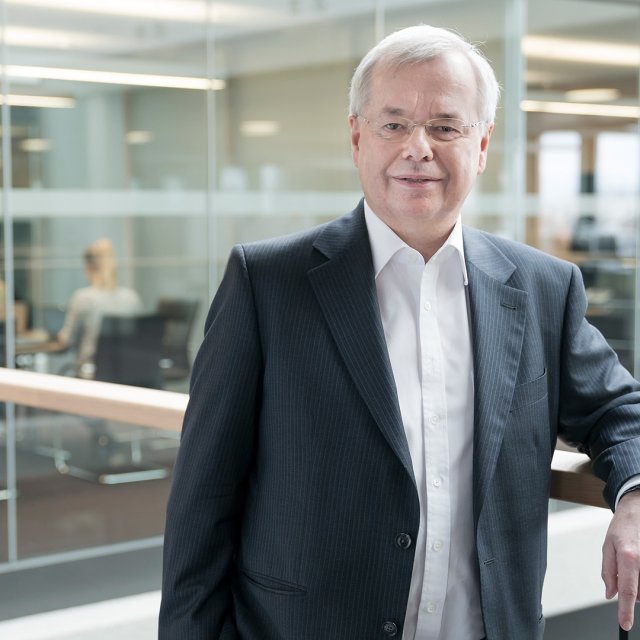
Innovation is the motor of society and the economy − and initiatives like the Give a Breath Challenge drive it ahead. Those who took part have demonstrated that with creativity, commitment and tenacity, possibilities for helping save people’s lives can be created quickly. I would like to say a big thank you to them!
/Ralf-Wehrspohn.jpg/_jcr_content/renditions/cropped.square.jpg./cropped.square.jpg)
I am particularly pleased with the good partnership with Munich Re and all others involved, whose commitment and ideas within the framework of the Give a Breath Challenge have made it possible to take a major step forward in overcoming the medical crisis.
Timeline and next steps:
March 2020
Launch of Challenge
April 2020
Announcement of Nominees for shortlist
May and June 2020
Further elaboration and optimisation of the solutions nominated to technical and medical requirements. Production of testable prototypes and validation on suitable test benches. Build up network of realisation partners
July 2020
Announcement of the winners
Planning of pilot projects with global network partners
August 2020
First deployment in coordination with interested governments
What the Give a Breath-Challenge was looking for
Munich Re and Fraunhofer were looking for feasible and digitally distributable construction drawings and blueprints for emergency ventilation equipment. This emergency equipment is to be used for the treatment of "non-intensive-care COVID-19 patients" in the event of a disaster. By disaster we mean the "worst case scenario", where the capacity of the local health systems is no longer sufficient and patients therefore face immediate danger to life and limb. This equipment is meant for emergency local treatment of “non-intensive-care COVID-19-patients” to reduce demand for hospitalisation.
The challenge was split into three categories. The first category was for designs for non-invasive lung ventilators and oxygen concentrators, the second for the development of non-invasive respirator masks, and the third for the provision of information on the use of the equipment developed and basic knowledge on Covid-19 for additional support staff needed. With these three components, a complete respirator system can be set up. It has to be possible to produce the equipment anywhere in the world using 3D printing or other fast manufacturing processes. The primary aim is to create the technological basis for the rapid local supply of ventilators to cope with imminent shortages in the local emergency treatment of Covid-19 patients and mitigate the impact of the pandemic for people affected worldwide.
Equipment to be piloted in South Africa
The digital blueprints for the ventilators and masks, including information on their manufacture, assembly and use, are to be made available to governments and partners throughout the world to enable them to be produced and used locally. The digital handbook for the treatment of Covid-19 patients will also be globally accessible via an app. This approach will enable severely affected regions to receive support more quickly and independently of international supply chains.
A plan for working with Stellenbosch University in South Africa to pilot the equipment designed has already been developed. Discussions on piloting are currently taking place with the Faculty of Medicine and Health Sciences at Stellenbosch University and the Fraunhofer Innovation Platform (FIP) at Stellenbosch University.
Support group from industry and science
Judging Committee:
- Munich Re Board Members: Dr. Torsten Jeworrek, Dr. Thomas Blunck
- Fraunhofer Board Members: Prof. Ralf B. Wehrspohn, Prof. Alexander Kurz
- Sartorius Stedim Biotech GmbH: Prof. Oscar-W. Reif, Chief Technology Officer Corporate Research
- Siemens Healthineers: Peter Schardt, Chief Technology Officer
- Chairman of the DIN advisory boards NARK and NAMed: Prof. Johann Weidringer
- Drägerwerk AG & Co. KGaA: Dr. Dr. Karsten Hiltawsky, Head of Technology and IP
- BMW Group: Dirk Hilgenberg, Senior Vice President Production Systems
- EOS GmbH: Dr. Marco Nock, Director Innovation Management
Want to get started?
/_MG_6343b.jpg/_jcr_content/renditions/original./_MG_6343b.jpg)
/martin_2012x2012.jpg/_jcr_content/renditions/original.image_file.120.120.file/martin_2012x2012.jpg)